Product Description
Iroda CT-630 Torch:
Iroda's CT-630 High Output Butane Torch is a heavy duty torch suitable for a variety of applications, such as plumbing, soldering and welding. It is also perfect for smaller applications that requires a concentrated flame in tight areas, such as brazing and welding. The CT-630 torch is also perfect for many other applications such as working on hobby models, appliances, small engines, household and commercial repairs, arts and crafts, audio systems, automotive and marine electrical repairs and jewelry work. The list goes on and on.
Features:
- Precision Flame Control (Adjustable Airflow)
- Maximum Temperature of 1300°C (2400°F)
- Attachable Tabletop Stand for Hands-Free Use
- Adjustable Gas Flow Control Valve
- Safety Latch Trigger
Iroda CT-630 User Manual (click here)
Soldering Vs. Brazing:
Soldering and brazing are both processes used to join metal pieces together, but they differ in terms of temperature, materials used, and the strength of the joint they create. Here’s a breakdown of the differences:
1. Temperature:
- Soldering: Operates at lower temperatures, typically below 840°F (450°C). The heat used is sufficient to melt the solder (a filler material), but not the base metals being joined.
- Brazing: Requires higher temperatures, usually above 840°F (450°C) but below the melting point of the base metals. The filler material melts and flows between the pieces, bonding them together without melting the base metals themselves.
2. Filler Materials:
- Soldering: Uses a soft filler metal (typically lead, tin, or a combination of both, or lead-free alternatives). This filler has a low melting point, which is why soldering is done at lower temperatures.
- Brazing: Uses a harder filler metal, such as brass, bronze, silver, or aluminum alloys. These materials have higher melting points, which is why brazing requires more heat.
3. Strength of the Joint:
- Soldering: Generally creates weaker joints compared to brazing. Soldered joints are typically used in electrical and plumbing applications where high strength is not required. However, they provide excellent electrical conductivity and airtight seals.
- Brazing: Creates stronger joints that can withstand higher loads and stresses. Brazed joints are often stronger than the base metals themselves, making them suitable for structural and load-bearing applications.
4. Applications:
- Soldering: Commonly used in electronics, circuit boards, and plumbing for joining copper pipes. The lower temperatures involved make it ideal for delicate components that could be damaged by higher heat.
- Brazing: Typically used in HVAC, automotive, aerospace, and metal fabrication industries. It’s ideal for joining dissimilar metals (like copper to steel or aluminum to brass) and is often used where stronger, more durable joints are necessary.
5. Method:
- Soldering: Involves melting the solder and allowing it to flow into the joint between the parts through capillary action. The parts themselves are not melted.
- Brazing: Also relies on capillary action to pull the molten filler metal into the joint, but due to the higher temperatures, brazing results in stronger bonds and often requires more skill and heat control.
6. Heat Sources:
- Soldering: Uses relatively low-heat sources such as soldering irons, small propane torches, or electric heat guns.
- Brazing: Requires higher-heat sources like oxy-acetylene torches, MAP/Pro gas torches, or furnaces capable of reaching higher temperatures.
7. Metallurgical Bonding:
- Soldering: The solder metal does not chemically bond with the base metals; it simply covers them, creating a mechanical connection.
- Brazing: The filler metal bonds metallurgically to the surface of the base metals, which is why brazed joints are generally much stronger.
Summary:
- Soldering is done at lower temperatures, with softer filler materials, and is used for delicate work like electronics and plumbing. The joints are weaker but are sufficient for non-load-bearing applications.
- Brazing is done at higher temperatures with stronger filler materials, creating stronger joints suited for structural applications and metalwork.
Specifications: | ||
Length | 6.6 in. (167 mm) | |
Dimensions: | Width | 1.6 in. (40 mm) |
Height | 3.0 in. (76 mm) | |
Length | 6.6 in. (167 mm) | |
Dimensions (w/LEC-60): | Height | 8.6 in. (218 mm) |
Grip Diameter | 2.0 in. (50 mm) | |
Base | 3.1 in. (80 mm) | |
Weight: | Empty Tank | 8.1 oz (+-) 0.07 oz (CT-630) |
(CT-630+LEC-60)/12.1 oz (+-) 0.07 oz | ||
Flame Temp: | ≈ 2400 ℉ (1300 ℃) | |
Operating Time: | Mid Setting (with LEC-60) | 50 min. |
Flame Length: | Mid Setting | 1.6 in. (4 cm) |
High Setting | 3.5 in. (8.89 cm) |
Warranty
1 Year Warranty on Normal Usage!Product Videos
Custom Field
Product Reviews
Write a Review
×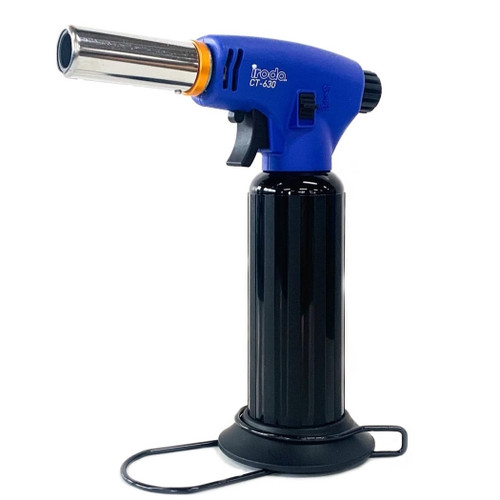